As the name suggests, heat sealing machine seals materials by applying heat and pressure. In other words, you heat the sealing tool, apply heat and pressure to the material, stop the heat but keep the pressure, let the material cool, and it bonds. I’ll give you a complete breakdown of how it works and what factors affect the quality of the seal.
What is Heat Sealer
A heat sealer works by using heat and pressure to seal materials. Think about when you burn something made of plastic with a lighter, melt it, and stick it to something. When it cools down, the bond gets strong. I’m sure you’ve done that in your daily life. The working process of a heat sealer is similar to the example I just gave you. When a bag is put between two jaws, heat and pressure are applied. This melts the plastic layer on both sides of the seam and bonds them together. When it cools down, it gets stronger.
If we categorize heat sealers, we can divide them into many types. They include hand held heat sealers, direct heat sealers, manual heat sealers, foot-operated heat sealers, heat sealers with a cutter, vacuum heat sealers, and ultrasonic heat sealers. They are all different in terms of how they seal.
Heat sealers are used in many industries. Some examples are pharmaceuticals, agricultural products, electronics, tamper-evident packaging, and food and beverage. Heat sealers are popular in many industries because they use heat and pressure, which makes the seal strong.
Working Process of Heat Sealer
Heat sealers can be used with plastic film, composite materials, foil, and kraft paper.
There are heated bars, wires, or jaws that heat up the package. When the materials are positioned, the heat sealer heats the sealing jaws. And at the same time, the sealer would apply pressure to the materials. The sealing jaws close and clamp the materials together. While the jaws are clamped together, the materials are under pressure. The heat goes through the layers. The layers melt and bond.
The dwell time depends on the materials and the type of heat sealer you’re using. It can range from fractions of a second to several seconds. Even though it might seem like a small change in time, it can make a big difference in the quality of the seal. If the dwell time is too short, the material may not melt completely. That will give you a weak or inconsistent seal. On the other hand, if the dwell time is excessive, the material may over-melt. This will weaken the material and affect the strength of the seal. Or even cause the material to deform or leak.
This is a critical step in the heat sealing process. It ensures that the material reaches the right temperature and consistency for sealing.
After you apply heat and pressure for a while, the heat stops but the pressure stays on until the materials cool down. They need some time to cool down and solidify the bond between the materials. If you release the pressure too soon, the seal may not be set.
The dwell time and the cooling time are two essential parts of the process.
Types of Heat Sealing
Hot Bar Sealing
It uses one or more heated bars to contact the material to heat the material and form a bond. It provides a consistent heat source for a set period.
Impulse Heat Sealing
Impulse heat sealer is one of the most popular heat sealing machines. It uses short bursts of electric current to quickly heat the sealing area. And it has one or two heating elements made by Nichrome. The heating elements are not continuously heated, heat is generated only when electric current flows through the sealer wire. That makes the impulse heat sealer safer, reducing the accidental burns.
Heat sealers use only a pulse to provide heat for a few seconds, which makes them suitable for thin materials.

Continuous Heat Sealers
It uses moving belts. The packaging bags are sealed as they move along the conveyor belt.
Suitable for high-volume production.

Constant Heat Sealers
Constant heat sealers keep both jaws at a consistent temperature. Once you turn the machine on, the heat sealers use power. They have good heat penetration. This is great for sealing thicker materials that require a consistent high temperature. Things like coated Kraft papers, mylar, and waxed paper.
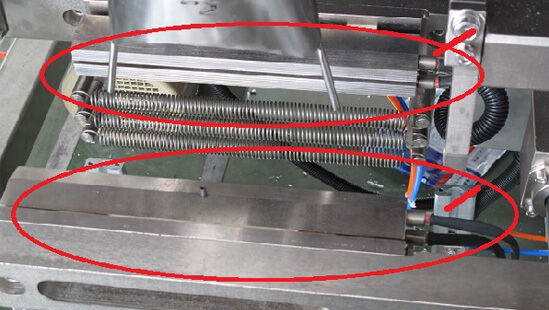
Foot-Operated Heat Sealers
They are controlled by a foot pedal, faster than hand-operated heat sealers. You can do other tasks with your hands.
Ultrasonic Heat Sealers
Ultrasonic sealing uses high-frequency vibrations to create seals. They are ideal for sealing temperature-sensitive materials, widely used in medical and pharmaceutical industries.
Hot Wire Sealing
The heated wire can not only cut the material but also melt the edges to form a seal. This process is quick and efficient.

Factors Influencing Heat Sealer Work
As we’ve already discussed the impact of dwell time on the performance of heat sealing machines, there’s no need to go further on that. Instead, let’s focus on other factors that influence the work of heat sealing machines.
Temperature
Different thermoplastic materials have different melting points. That means you need to adjust the temperature based on the nature of the material. If the temperature is too high, it can cause the material to over-melt and damage the package. If the temperature is too low, the seal may be weak or incomplete. That’s why you need to know the relevant information about the material you’re sealing.
For example, when you’re sealing polyethylene bags, you’ll need a lower temperature than if you were sealing aluminum foil bags. Polyethylene has a heat-sealing temperature of 140 degrees Fahrenheit (or 76.6 degrees Celsius).
Contaminants
Water, dust, or other solid particles on the heat sealer can affect the quality of your seal. This can make your seal uneven or even create gaps. Make sure you clean your sealer regularly.
Pressure
You need to apply uniform and consistent pressure during the sealing process. If the pressure is insufficient or inconsistent, it will end up with an uneven seal or even gaps in the seal. That’s why it’s important to apply consistent pressure. That will give you a strong, reliable seal
Material Thickness
Another important factor is the thickness of your material. Thicker materials require more time and more heat to get a strong seal. Thinner materials may require less time and less heat. If you don’t take the thickness of your material into account, you might not get a good seal.
Conclusion
This article can give you a more detailed understanding of the operation of heat sealing machines. For example, you need to carefully consider factors such as dwell time, material thickness, and pressure. If you manage these things well, you’ll get a strong, reliable seal.